BIM/VDC Technology
IMC provides Virtual Design & Construction technology to drive our workflow from Preconstruction to Construction delivering predictable results.
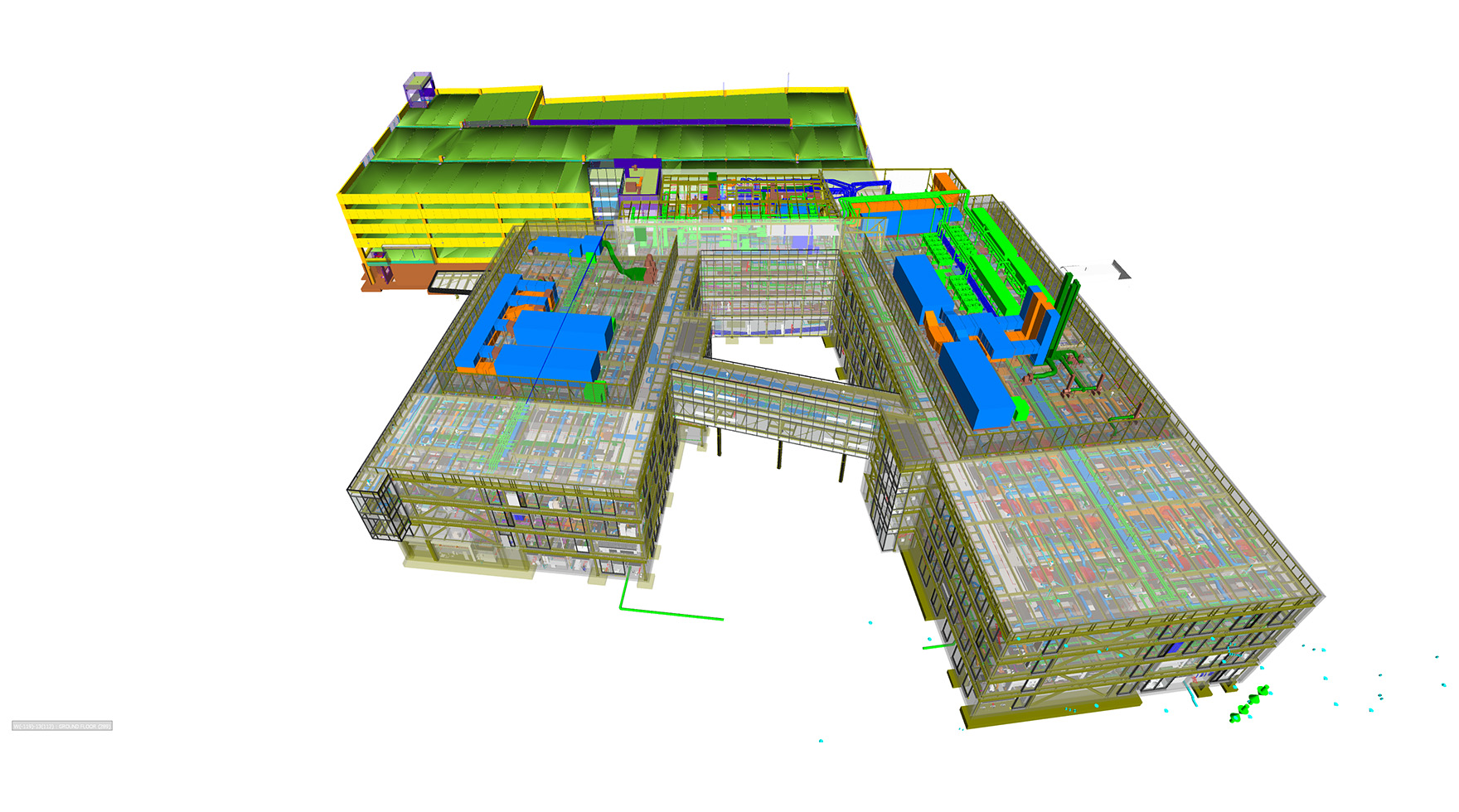
Visualize, Analyze and Optimize
IMC was a pioneer adopting BIM/VDC and integrating it into all aspects of our workflow – early in Preconstruction, throughout Construction, Project Closeout, and Facility Management. IMC has a fully staffed, Autodesk Certified VDC Department. In addition to this VDC team, we have trained our estimators and field staff on virtual models and technologies. This allows us to visualize, analyze, optimize, and communicate our pricing, procurement, project logistics/schedule, coordination, and safety controls. Our use of VDC affords a holisitic view of the project which provides significant, quantifiable cost and schedule savings. Team sharing of the models and cloud access for all project stakeholders facilitates collaboration and timely solutions.
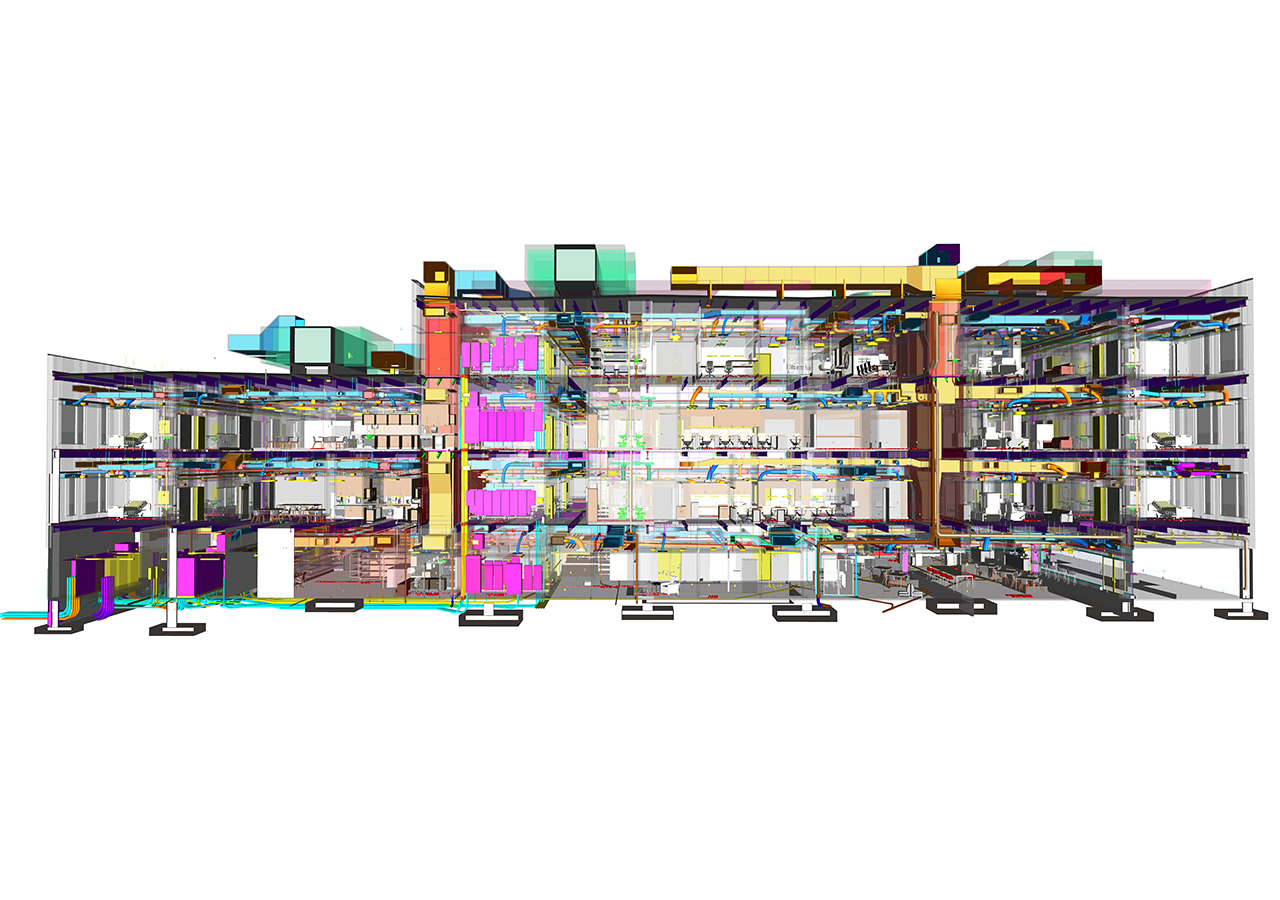
Collaborative & Integrated Technology Drives our Workflow
Our budget pricing is derived from 3D models. Our estimator’s takeoffs are automated from these models and their time is spent talking to subs, analyzing pricing options, and not taking off drawings/pdfs by hand or electronically item by item. This model-based estimating allows a holistic view of the project and facilitates communication on material costs, locations, alternates, and extents. This process results in quicker pricing and communication of Base Bids as well as multiple alternates, design, and cost saving options. We utilize this process early in preliminary design and continue through any design changes through construction.
Using various technologies IMC captures, models, and communicates our projects’ existing conditions, above & below ground. Utilizing as built drawings, drones, current satellite imagery, soil borings, 360 Cameras and Laser scanning, we model and analyze the current site conditions, even before surveyors are engaged. This progresses into preliminary design by modeling the proposed site layout/ infrastructure and allows early cut/fill analysis, hardscaping quantities & visualization to verify design intent. This upfront design work by IMC is valuable for feasibility studies/early budgeting and allows quick comparative analysis of design options and can uncover challenges before paying design fees.
We preempt delays and rework in the field and accelerate project completion by utilizing our digital twin 3D and 4D computer models of existing and proposed conditions for coordination, clash detection, and construction schedule simulation. This collaborative process allows designers and subcontractors to input solutions to potential issues during weekly model review/coordination meetings. The schedule simulation allows all stakeholders, including regulatory agencies, to understand what will be happening on site and when – giving insight into site logistics and safety controls. The planned schedule is updated weekly with the actual schedule to track against progress, delays, and opportunities to make up time.
Immediate and downstream use of the models we use for preconstruction and coordination is the visualization aspect. From renderings, video fly-bys, and walkthroughs to immersive/ interactive Virtual and Augmented Reality, we use these tools to validate design intent, inform our subcontractors, support regulatory requirements, create virtual mockups, engage and get buy in from end users, and support marketing initiatives. Cloud-based technology facilitates access to this regardless of skill set, proprietary software, and can be viewed across computers and various types of devices. This also allows the end users to interactively walk through the models and isolate and hide geometry to focus on areas of interest.
- Quantitative Model Based Takeoffs
- 360 Virtual Pre Bid Walk
- Sitework Cut Fill Evaluation in Preconstruction
- Site Utility vs Rock Elevation Review
- Cost Savings Design Options Analysis
- Drone – Existing Topography Capture
- Design Efficiency Metric Review
- Visual Scope & Takeoffs for Bid Packages
- Laser Scan – Existing Conditions Capture
- Design Model Constructability & Coordination Review
- Site Logistics – Plans, Visuals, Animations,
- Virtual Reality Design Reviews
- Building Envelope Virtual Mockups
- Trade Model Detailing & Coordination
- MEP FP Model Conflict Review & Coordination
- Façade Model Conflict Review & Coordination
- 360 Virtual Progress Walks
- Model-Based Change Management Review & Quantification
- Augmented Reality QA QC Reviews on Site
- Critical Path Schedule Progress Tracking
- Drone – Envelope QA QC Inspections & Documentation
- Laser Scan – New Construction QA QC Review
- Laser Scan – Floor Flatness QA QC Review
- 360 As Built Documentation – Photo & Model-Based
- As Built Model Turnover
- FM CMMS Database Integration
Capitol Seniors Housing Exton 4D Modeling